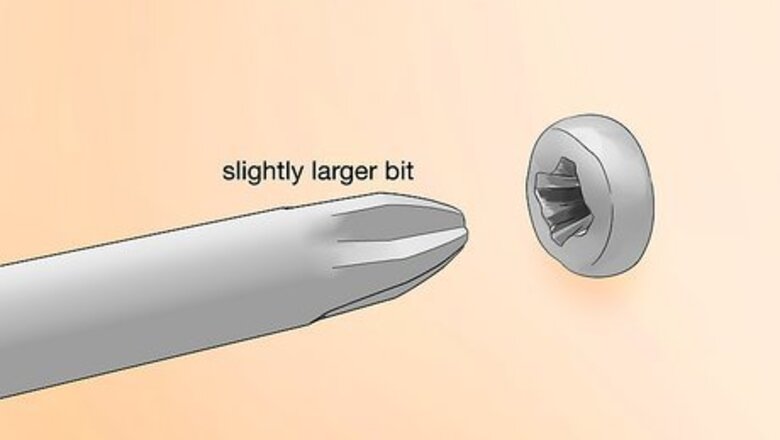
views
- Use a screwdriver that’s a different style or larger size than the screw to get an extra grip on it.
- Set a rubber band or duct tape over the screw head to help your screwdriver catch on the threadings easier.
- Apply friction drops to the screw head so the screwdriver gets a better grip.
- Grip the screw head with a pair of pliers if it’s raised above the surface.
Try using a different screwdriver.
A different size or style of screwdriver can get a better grip. If you’re trying to get a stripped Phillips-head screw out, pick a screwdriver with a slightly larger bit. Apply firm pressure so the screwdriver catches on the stripped head and try loosening it like normal. If that doesn’t work, then switch to a flathead screwdriver since it can fit into the slots better. If a different screwdriver doesn’t catch, then stop trying to use it so you don’t damage the screw even more. If you’re using a screwdriver bit in a drill, then try unscrewing with the next largest bit size to try getting a better grip.
Place a rubber band over the screw head.
The rubber band fills the gap so your screwdriver catches. Lay a thick rubber band over the top of the screw head. Press your screwdriver down firmly and try turning it as normal to loosen the screw. If the screw still doesn’t budge, try using a screwdriver with a slightly larger head so it catches better. Rubber bands also provide a non-slip surface so your screwdriver doesn’t move around on the stripped screw.
Stick a piece of duct tape over the screw.
A layer of duct tape can give you extra friction to turn the screw. Cut off a piece of duct tape and place it directly over the screw that’s stuck. Put your screwdriver into the screw and try turning it counterclockwise until it loosens up. The tape fills in some of the gap between the screw and your screwdriver so it has a better grip. Alternatively, try placing steel wool over the screw head and firmly pressing your screwdriver into the slot to get better traction.
Grip a raised screw head with pliers.
Pinching the sides of the screw will make it easier to turn. Open your pliers and grip the sides firmly. Make sure your pliers don’t slip off of the screw as you turn it counterclockwise. Keep turning the screw until you can remove it completely. Try filing the sides of the screw so they’re a little flatter so your pliers don’t slip off as easily.
Tap the screw with a flathead screwdriver and hammer.
Hitting the screwdriver makes a new slot in a soft screw. Place the tip of a flathead screwdriver on the top of the stripped screw. Lightly tap the end of the screwdriver’s handle 2–3 times with your hammer so it can dig into the screw head. Without lifting your screwdriver up, try to turn the screw to see if you can loosen it. If you’re trying to remove a rusty screw that’s stripped, try spraying a rust penetrant before tapping the screwdriver to help break apart the corrosion.Remove a Stripped Screw Step 5Bullet1.jpg
Apply friction drops to the screw.
Friction drops add an abrasive so your screwdriver can catch easier. Put 1–2 drops into the middle of the stripped screw and immediately put your screwdriver into the slot. Since the drops fill the gap between your tool and the metal, just turn the screwdriver counterclockwise to loosen and remove the screw. You could also try using an abrasive powder like salt or sand to prevent your screwdriver from slipping.
Drill into the screw with a left-handed bit.
Running a left-handed bit in reverse digs into the screw for a good grip. Install a bit that’s just smaller than the screw’s diameter on your drill. Lightly press the end of the drill bit into the middle of your screw. Set your drill to reverse and slowly squeeze the trigger. The tip will catch on the damaged screw and continue to loosen it. Avoid using a right-handed drill bit since it won’t properly catch on the screw head.
Use a screw extractor.
A screw extractor cuts into your screw so you can pull it out. Screw extractors are specialty drill bits with one end that cuts and one end that bites into the metal. To use the extractor, install the cutting bit on your drill and run it in reverse to bore into the middle of the screw. Then, flip the extractor to the pointed side and drill into the screw to loosen it. Screw extractors are reusable, so keep one in your toolbox in case you run into another stripped screw.
Cut a new slot in the screw with a rotary tool.
Cutting a new slot makes a flathead screwdriver get a better grip. Load a cutting disc onto a rotary tool that’s made for cutting into metal. Position the disc vertically and turn on the tool so it starts spinning. Lightly press the tool into the screw head to make a straight line across the surface. After you cut a line in the screw, fit the end of a flathead screwdriver into the slot and turn it counterclockwise. Rotary tools create sparks, so wear safety glasses and avoid working near anything flammable.Remove a Stripped Screw Step 9Bullet1.jpg
Weld a nut onto the screw.
Attaching a nut lets you hold the screw with a wrench. Use a nut that’s about the same size as the screw head’s diameter. Hold the nut against the top of the screw head, and start welding the bottom of the nut to attach it. After you have the nut secured, just grip it with a wrench and turn it counterclockwise to remove it completely. Be sure to wear proper welding gear, like a welding mask, gloves, and an apron.Remove a Stripped Screw Step 10Bullet1.jpg This works best for screws attached to metal since welders can leave burn marks on wood.
Comments
0 comment