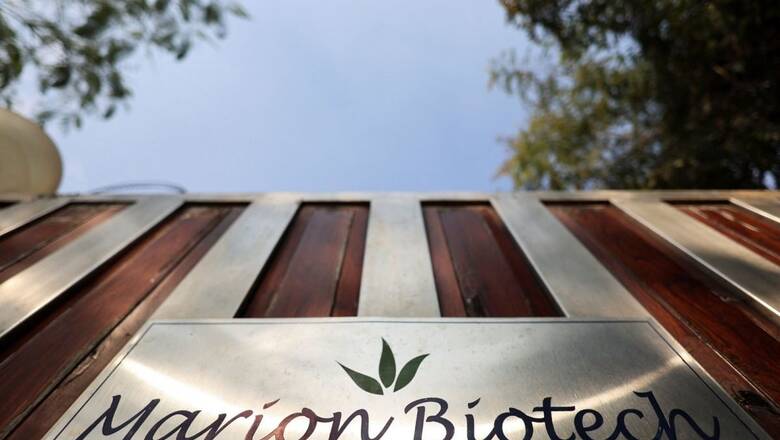
views
Rusted equipment, seepage in walls, unhygienic premises, missing batch numbers, ill-maintained room temperatures and more — a probe into the manufacturing unit of Uttar Pradesh-based Marion Biotech has found more than 30 loopholes.
Marion Biotech, which is at the centre of a row over the death of children in Uzbekistan, was raided by the state and central drug controllers on December 27 after Uzbekistan shared the details of the issue with the Union Health Ministry. The production licence of the Noida-based pharmaceutical firm has been suspended while the test results of its controversial cough syrup are awaited, an Uttar Pradesh drug official said on Thursday.
The spokesperson of Marion Biotech, in a reply to the email send by News18, said: “Before responding to your query, it is submitted that we have already sent reply to the concerned authorities. Marion Biotech Private Limited has adhered to the approved normative documents and process while manufacturing the syrup in question. We do not agree with the findings that the residue of Ethylene Glycol was present in the Doc 1 Max Syrup. We are cooperating with Government of India in the testing of the control samples. The results of the same are still awaited. We are extending all our support for the fair investigation on the issue.”
The investigation report — prepared by the Food Safety and Drug Administration Department in Lucknow on January 9 — reflects “very poorly” on Marion, a top government official privy to the investigation told News18.com.
“While Marion Biotech was procuring propylene glycol from its approved vendor, several flaws were highlighted during the investigation,” said the official.
Investigators found that the invoice copy of procurement of propylene glycol did not bear any drug licence and the product supplied bears no batch number among other important details.
“The sales invoice by Maya Chemtech had no mention of lot number or pharmacopoeial specification of propylene glycol. Also, the company was unable to produce copy of manufacturer’s certificate of analysis,” the government official told News18.com.
“For the manufacture of Dok-1 Max Syrup, which has allegedly killed children in Uzbekistan, the drugmaker was found to have used propylene glycol from an unapproved vendor as per the investigation report,” the official said.
He added: “In fact, the report mentions that the firm has informed the inspecting team that they had not tested propylene glycol for the impurity of diethylene glycol and ethylene glycol.”
The official said no tests for the presence of diethyl glycol and ethyl glycol were performed as per certificate of analysis of propylene glycol by the firm.
Essential Equipment Not Working, Drugs Kept in Corridors
The investigators also found that the thermohygrometer, a device used to determine humidity to control moisture level of the room, was not working.
“Investigators also found that the walls of the empty capsule storage room had seepage and was not maintained in a hygienic condition. The manufacturing room also had seepage,” he added.
The firm had also failed to provide essential space for storage of finished goods at the required temperature. “The team also found that multiple batches of finished medicines were kept in the passage stocked for dispatch for a very long time and there was no record of temperature of the corridor where these batches were kept.”
Another discrepancy was that the stand of the air purifier — called laminar air flow to move particles away from the filling area — was found rusted.
No PPE Kits, Unhygienic Conditions
The report, the official said, also mentions that no PPE kits (personal protective equipment) were provided to workers for various types of solvents.
“The investigators found only one changing room at the ground and it did not have any environment control measure, thus breaking another protocol,” the officer said.
The same room was being used for wearing gowns by workers working in the manufacturing of the non-critical area as well as for workers working in core manufacturing area such as tablets, injections, liquids and ointments.
“There were no provisions found for garment change just before entry to respective manufacturing section.”
He added that “the sink and drain in the change room were not as per the protocol and it was not maintained in a hygienic condition. Also, the door of this changing room was rusted”.
Epoxy flooring provided in oral liquid filling and manufacturing rooms was found “broken at several places thus making it difficult to clean”.
The ointment manufacturing room, ointment filling room, oral granules manufacturing room, and ALU/ALU blister packing room was directly opening into a common corridor due to which “the differential pressures of these rooms were found out of specified limits”.
Read all the Latest India News here
Comments
0 comment