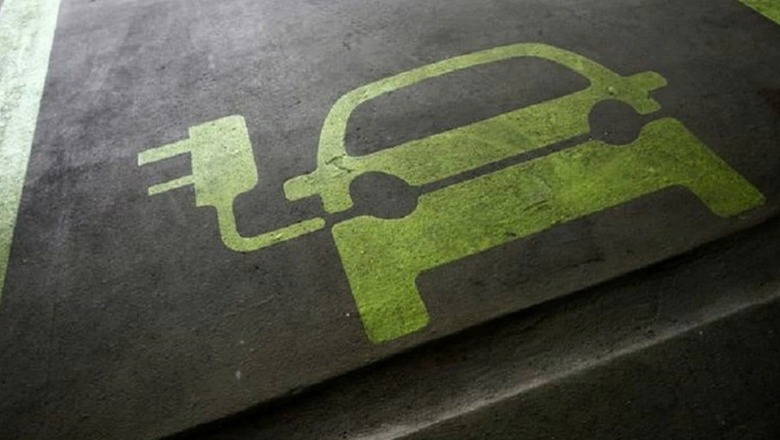
views
By 2030, India could have 145,000 tonnes of used lithium-ion batteries that need to be recycled owing to the continuous development of the electric vehicle (EV) industry and increasing consumer demand. Experts say it is a problem that cannot be ignored.
As this industry evolves and becomes more important in tackling climate change, a new difficulty will emerge – obtaining the minerals required to manufacture electric vehicle batteries.
Lithium, nickel, cobalt and copper used in those batteries were all extracted from the Earth at one time. Much of that mining is now concentrated in countries like Russia, Indonesia and the Democratic Republic of the Congo, where environmental oversight is inadequate, labour standards are often lax, and the mining business has a history of fuelling disputes with local populations.
Experts believe India will have to improve recycling of EV batteries as they die to reduce the demand for new mining. While just a limited number of EV batteries have actually been retired from the road, millions of tonnes of batteries are likely to be retired over the next few decades.
Those batteries have the potential to handle a major portion of the EV industry’s future mineral needs, but better recycling processes and government regulations to support them are required to avoid sending them to landfills, say experts.
IN INDIA
India, with its limited stocks of lithium, graphite, cobalt, and nickel, will benefit from recycling EV batteries.
A majority of India’s lithium-ion batteries are now imported from China. Recycling will lower the cost of EV batteries, accelerating the adoption of electric vehicles in Asia’s third-largest economy.
According to a study conducted by NITI Aayog and the Rocky Mountain Institute (RMI) in the United States, India might account for approximately a third of the worldwide demand for EV batteries by 2030, with the country’s battery industry expected to reach $300 billion.
However, the current need to develop a comprehensive battery recycling ecosystem stems from the fact that recycling batteries for electric vehicles is tougher than recycling batteries for mobile phones and other devices.
Earlier this year, it was reported that Attero Recycling, an electronic waste recycling company, has revealed intentions to invest around Rs 300 crore to increase its lithium-ion battery recycling capacity to 11,000 metric tonnes per annum by October 2022, up from 1,000 metric tonnes per annum now.
India’s new production-linked incentive programme also gives original equipment manufacturers the opportunity to ensure a robust domestic metals sourcing network is in place by the time local cell manufacturing takes off. Industry experts have been claiming that EV batteries would be cheaper if they were made in India.
ACROSS THE WORLD
According to the International Energy Agency (IEA), the globe has enough capability to recycle 180,000 metric tonnes of dead electric vehicle batteries each year. In comparison, all electric vehicles sold in 2019 will produce 500,000 metric tonnes of battery waste. Additionally, the IEA projects that by 2040, there will be 1,300 gigawatt-hours of expended batteries.
That waste could be a significant source of minerals if recycling can be ramped up. The IEA forecasts that by 2040, recycling could meet up to 12% of the EV industry’s mineral needs in a sustainable development scenario, where the EV market grows at a rate consistent with keeping global warming below 3.6 degrees Fahrenheit (2 degrees Celsius).
However, if the same climate scenario is combined with a more optimistic set of recycling assumptions, recycling might become considerably more important.
According to a report commissioned by Earthworks, if we assume that 100% of dead EV batteries are collected for recycling and mineral recovery rates, especially for lithium, recycling could meet up to 25% of the EV industry’s lithium demand and 35% of its cobalt and nickel needs by 2040.
Read all the Latest Auto News and Breaking News here
Comments
0 comment