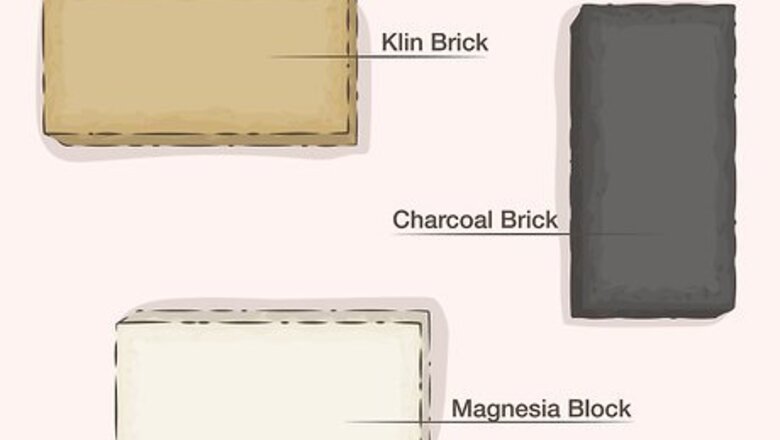
views
Gathering Materials
Use any type of soldering brick. These are designed to prevent heat loss and withstand a great deal of heat. Kiln bricks, magnesia blocks, or charcoal bricks are all common options.
Purchase gold solder. Any metal alloy designed to melt and join metal together is called a "solder," but most solders will not work to join gold. You can buy gold solder, designed for this purpose, as sheets, wire, or in 1 mm (~1/32 inch) chips. Cutting larger pieces of solder into chips is recommended, to make it easier to control the precise amount of solder being applied. Solder with a higher gold content is stronger, but takes more heat to melt. It is recommended for joining two pieces together. Use "plumb solder," "medium" or "hard" solder, or solder with 14 karat and above. Solder with a lower gold content will melt more easily, and is recommended for small repairs. Use "repair solder," "easy" solder, or solder below 14 karat. Check the label before buying pink or rose gold solder, as it may contain highly toxic cadmium.
Select a precision torch for melting the solder. A small oxy-acetylene gas torch is a good choice, but butane or other high-temperature torches will work as well. Soldering irons are not recommended for precious metals or other high-temperature soldering tasks.
Find an appropriate flux. Before soldering gold, or most other metals, a chemical product called "flux" should be applied to clean the metal's surface and help the soldering process go smoothly. Find a flux at a hardware or jewelry store that is safe for use on precious metals. This is sometimes called "brazing flux" due to the technical term for this high-temperature joining process. Flux comes in paste or liquid form, or as a powder that creates a paste when mixed with water. While brazing is technically a different process than soldering, even jewelers usually call this process "soldering." A flux labeled "soldering flux" may work, but check the packaging to see if it is appropriate for gold.
Ventilate the work area. Use fans or open windows to create a light breeze over the work area, moving potential fumes away from you. Strong breezes may make the soldering process more difficult, due to the cooling effect.
Acquire copper tongs and tools for holding the gold in place. Copper will not corrode in the acidic pickle solution described below, unlike steel. You'll also need any tool that can hold the gold objects in position, usually tweezers. A clamp or vise can also be used, but tighten lightly to avoid bending the gold. The other tools do not need to be made from copper.
Follow safety precautions. Safety goggles are vital to protect your eyes from molten droplets. A thick canvas apron is recommended to prevent burns on your clothing. Roll up long sleeves and tie back long hair as an additional precaution.
Set up one water bath and one pickle bath. Set a container of water out for cooling and rinsing the gold. Purchase a "pickle" solution for cleaning oxidization off metal, and prepare it according to the instructions on the packaging. Most pickle manufacturers sell it as a powder, which can be prepared in small amounts by dissolving with water and heating. Never place the pickle solution in a steel container, or put it in contact with a steel utensil. Never heat pickle in a microwave or container that you intend to use for cooking. The pickle can leave an unpleasant smell or even traces of harmful materials.
Joining the Gold
Clean gold thoroughly. The gold surfaces to be joined need to be clean of dirt and grease for the solder to chemically bond them together. Soak them in the pickle solution briefly to remove surface contamination, then rinse in water to remove the acid. Scrub the surfaces with detergent or soap for additional cleaning. Some people neutralize the acidic pickle by adding baking soda to the rinse water, but this is not necessary unless your pickle is unusually strong.
Hold the gold in place. Place the gold objects on a soldering block, and hold in place with tweezers or a clamp. The areas to be joined together should fit together as closely as possible; this process cannot typically fill large gaps.
Apply a small amount of flux to the parts being soldered together. Flux will help remove additional impurities, and prevent discoloration to the surface. Applying the flux only where the pieces will be joined may reduce the amount of solder that flows to the wrong area, but some people prefer to apply the flux over the whole piece to minimize discoloration.
Heat the flux slightly. Use the torch to briefly heat the flux wherever you applied it, until the water boils away and leaves behind protective solids, which inhibit the formation of copper oxides. If you applied flux to the entire object, be sure to perform this step thoroughly before you add the solder.
Apply a small amount of solder and heat. Place a chip of solder on one end of the seam to be joined, and heat the surrounding gold objects. If you are using an appropriately high-temperature torch, you should be able to heat that area sufficiently to melt the solder without having to heat the entire object. Move your flame back and forth slowly as you heat, to apply the heat across the length of the seam to be joined. The solder should melt and flow across the seam, visibly joining the two sides together.
Treat the joined piece with water and pickle. Once the solder has flowed along the joint, and the metal surfaces have been heated sufficiently to join together, turn off the torch and let the gold cool. After a couple minutes, quench it further in the water bath. Use copper tools to lower the gold slowly into the pickle bath, and wait a few minutes for most of the discoloring fire-scale on the surface to be removed.
Make final adjustments if needed. Remove the gold from the pickle, rinse in the water bath, and inspect. You may need to polish or file off excess solder or fire scale to achieve the appearance you desire. The two gold objects should now be joined together with a strong bond.
Comments
0 comment